The Current Landscape and Key Challenges of Chemical Manufacturing Businesses in India
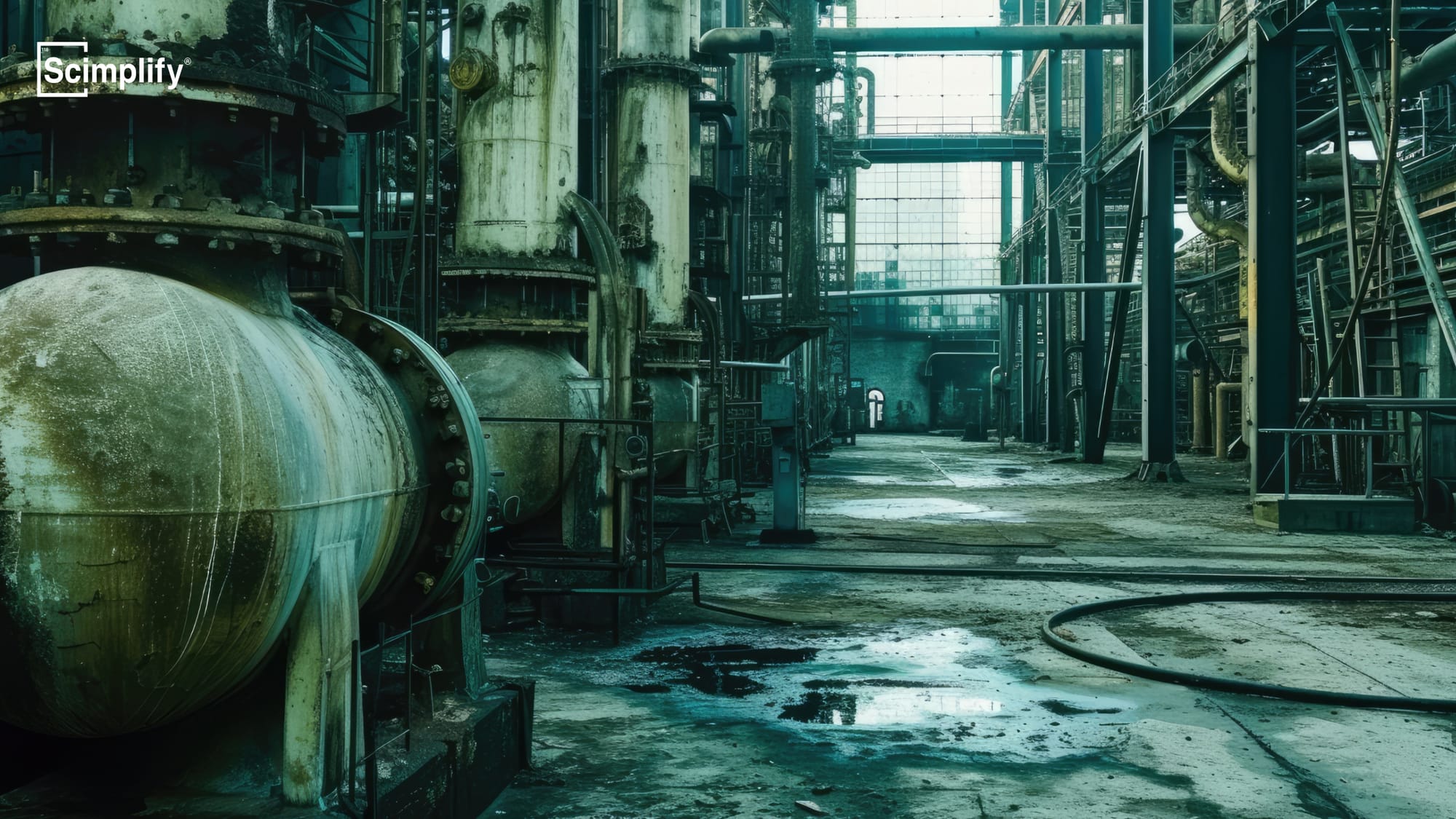
The Indian specialty chemical manufacturing industry is growing at a fascinating pace of 8.1% CAGR and is expected to reach $300 billion by 2030. As a result, the industry has seen a rise in investments, which has helped India become the sixth-largest producer of chemicals globally, contributing to 7% of its entire GDP.
This growth trajectory is driven by a confluence of factors, including increasing demand for specialty chemicals across industries like pharmaceuticals and agrochemicals and a shift towards localized production. India's thriving domestic market and cost-competitive manufacturing ecosystem position it as a global hub for chemical production.
However, some major challenges must be addressed by chemical businesses in India to sustain this growth trajectory and ensure the sustainability of small and medium-sized chemical manufacturers in the country.
Challenges Rivaling The Growth of India's Specialty Chemical Industry
To maintain its growth momentum and global competitiveness, the chemical sector in India must tackle multiple challenges. Understanding these hurdles and their implications is vital for stakeholders to implement strategies that reduce risks while driving innovation, improving efficiency, and expanding market opportunities.
1. Dependence on imported raw materials
India has seen significant growth in exports of chemicals with an AAGR of 12.8%, chemical exports, reaching $20.4 billion in FY2024. However, the country is still a net importer of chemicals, keeping it in a trade deficit. This dependency exposes manufacturers to global price volatility, supply chain disruptions, and geopolitical tensions, such as those experienced during the COVID-19 pandemic.
In fact, a March 2020 survey by the Institute for Supply Management (ISM) March 2020 revealed that nearly 75% of companies reported supply chain disruptions due to coronavirus-related transportation restrictions. This is a major challenge businesses must address because local raw material shortages raise costs and create uncertainty in production timelines, making it difficult to meet commitments to global buyers.
The solution lies in encouraging backward integration in the supply chain by acquiring or merging with raw material suppliers, setting up domestic chemical parks, and incentivizing local production through government support like subsidies and tax breaks. Diversifying import sources beyond China could also mitigate risks associated with geopolitical dependencies.
2. Compliance and sustainability challenges
Environmental regulations and sustainability requirements are becoming increasingly stringent. India's specialty chemical manufacturers must now adhere to international norms like REACH, OSHA, and GHS, as well as local pollution control regulations enforced by the Central Pollution Control Board (CPCB). However, compliance costs can be prohibitive, particularly for SMEs, which account for 30% of the industry.
Reports suggest compliance-related investments in pollution control equipment and monitoring systems can increase capital expenditure by 10-15%. Non-compliance risks are equally significant, with penalties, production shutdowns, and reputational damage being common consequences.
On top of this, global buyers are demanding greener production processes, adding pressure on manufacturers to adopt sustainable practices like zero-liquid discharge (ZLD) systems and renewable energy sources. This makes it challenging for smaller manufacturers to upgrade their plants and processes to meet this evolving landscape.
3. Underutilization of plant capacity
One of the most pressing challenges in the specialty chemical sector in India is the underutilization of plant capacity. Our study suggests that 30-40% of chemical manufacturing units in India operate below optimal capacity.
This inefficiency arises from several factors, including the inability to generate consistent demand, lack of market penetration strategies, and overinvestment in capacity without corresponding growth in downstream industries. Additionally, fragmented demand and a reliance on seasonal industries like agrochemicals exacerbate the problem.
To overcome this challenge, businesses need to generate demand for their products, thereby boosting their utilization rate and profitability. This is possible through ATOMS, a one-stop platform that helps solve the underutilization problem by assisting manufacturers in accessing global demand while offering businesses a reliable platform to discover and collaborate with them.
4. Huge talent, less technical expertise
Despite being a labor-rich country, India faces a significant shortage of skilled professionals in the specialty chemical industry. Businesses regularly highlight their struggle to find workers with expertise in advanced chemical processes, automation, and quality control. The lack of trained R&D personnel further limits the industry's ability to innovate and develop value-added products, which are critical for global competitiveness.
This skill gap is particularly acute in smaller firms, which often lack the resources to invest in training programs or attract top talent. To bridge this divide, companies must collaborate with academic institutions to create tailored skill-development programs. Additionally, government initiatives like the Skill India program could be leveraged to build a pipeline of professionals trained specifically for the chemical manufacturing sector.
5. Infrastructure and logistics bottlenecks
India's infrastructure shortcomings significantly hinder the growth of the specialty chemical industry. Poor port connectivity, inadequate warehousing facilities, and unreliable power supply are recurring issues that increase production and transportation costs.
According to a report, logistics costs in India account for 14% of GDP, compared to the global average of 8-10%, making Indian exports less competitive globally. The lack of specialized chemical storage facilities, such as temperature-controlled warehouses, further complicates logistics. This is particularly challenging for high-value specialty chemicals that require stringent handling and storage conditions.
This challenge can be solved through public-private partnerships (PPPs) combined with investments in industrial clusters to improve logistics infrastructure for chemical manufacturers, alleviating bottlenecks and enhancing the industry's global competitiveness.
Bringing Global Demand to Specialty Chemical Manufacturers in India
ATOMS is an all-in-one supply chain platform designed to connect Indian specialty chemical manufacturers with both domestic and global businesses. It serves as a bridge, enabling manufacturers to generate demand for their products while providing businesses seamless access to over 3,000 specialty chemicals from 150+ trusted manufacturers.
What sets ATOMS apart?
- Comprehensive support: From R&D to full-scale production, we cover every stage of the product lifecycle.
- End-to-end transparency: Enjoy complete visibility across all stages of the supply chain, ensuring trust and efficiency.
- Integrated solutions: By combining research, development, and production, we streamline processes under one cohesive system.
Whether you're a chemical manufacturer aiming to expand your market or a business seeking high-quality specialty chemicals with just a click, ATOMS is here to simplify your journey.
Final thoughts
The Indian specialty chemical manufacturing industry holds immense potential to establish itself as a global leader, driven by its robust domestic demand and cost-effective production capabilities. However, to fully capitalize on this growth, the industry must address critical challenges such as dependency on imports, compliance with stringent regulations, underutilization of capacity, skill shortages, and infrastructure bottlenecks.
Through strategic investments in backward integration, sustainability initiatives, skill development, and infrastructure upgrades, Indian manufacturers can overcome these obstacles and achieve long-term competitiveness on the global stage.